This paper introduces a practical approach for directly controlling a stepper motor using a programmable logic controller (PLC), as illustrated in Figure 2. The key benefit of this method is that it significantly reduces the system design workload, eliminates compatibility issues between different interface signals, and enhances the overall system reliability. The control system consists solely of a PLC and a stepper motor. As an industrial control computer, modern PLCs are becoming increasingly powerful, capable of handling not only basic switching logic but also closed-loop process control. They can also integrate with other computers to form multi-level control systems.
Thanks to the advanced capabilities of the PLC, various command pulse controllers from different systems can be managed through custom PLC programs. However, for functions like ring pulse distribution and power amplification, the PLC must meet two important requirements. First, it should support real-time signal refresh technology to achieve output frequencies of several thousand Hz or higher. This ensures fast ring pulse distribution, fully utilizing the speed response of the stepper motor and improving the system's responsiveness. Second, the PLC’s output ports must use high-power transistors to handle the high voltage and current pulses required by the motor’s phase windings.
It's important to note that PLCs with relay or thyristor-based output ports may not be suitable for direct motor control, even if their software can generate high-speed signals. This is because these devices cannot switch DC power quickly enough to provide the necessary pulse current for the motor’s windings. Therefore, they are not appropriate for direct control of stepper motors. PLC models such as the IP1612DC-220 from US IPM, which meet these requirements, can be used effectively for direct motor control.
The author successfully implemented this technique in the automatic bagging error compensation system of the ZXJ1000-C prestressed composite bag production line. In this system, the PLC receives the measured bag length error signal from a sensor, as shown in Figure 3. Based on the error and a pre-defined compensation algorithm, the PLC calculates the number of steps the motor needs to compensate and controls the ring pulse distribution through outputs Y9, Y10, and Y11. This allows the motor to rotate by sequentially energizing its three-phase windings, creating a rotating magnetic field. The motor’s rotation is then combined with the main drive train via a mechanical differential to correct the bag length error.
To protect the PLC’s output ports, a current-limiting resistor is added due to the low DC resistance of the motor. When the high-power transistors connected to Y9, Y10, and Y11 are turned on and off in the sequence Y9-Y9Y10-Y10-Y10Y11-Y11-Y11Y9-Y9..., the motor rotates forward. Reversing the sequence causes the motor to rotate backward. This operation follows a three-phase six-step pattern. Each step taken by the motor reduces the count in the ring pulse distribution program. When the count reaches zero, the distribution stops, waiting for the next error measurement input.

Figure 2: PLC Direct Control of Stepper Motor
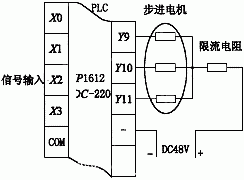
Figure 3: Specific Application Diagram
In conclusion, the error compensation system that uses a PLC to directly control a stepper motor demonstrates excellent performance, flexibility, and reliability. This system was recognized with the National Science and Technology Progress Award. The method of directly controlling the motor via a PLC reduces system design complexity, shortens development time, and offers significant value for practical applications within a certain scope.
medical transformer,adt transformers,lighting transformer,amp transformer
IHUA INDUSTRIES CO.,LTD. , https://www.ihuagroup.com